Using Oil Sensors for Refinery Plant Control & Control
페이지 정보

본문
Process sensors employ a critical position in the running of refinery plants, by offering essential facts on the structure of fumes existing in the process streams.
For information is essential for supervising and governing the refinery's efficiency processes, guaranteeing the security of the plant, and minimizing natural consequence.
The key function of monitors in oil refineries is to track and control the levels of hazardous gases in the pipeline. Such gases are often existing in the inputs and end-products, газовый анализатор and can harm to equipment damage, corrosion, and natural pollution if not correctly controlled.
Process analyzers enable refineries to identify these gases in real-time data, enabling operators to perform corrective moves to prevent these issues.
In addition to controlling hazardous fumes, sensors also utilize a crucial role in optimizing refinery operations. Through examining the make-up of the medium, operators can spot opportunities to improve efficiencies, minimize energy demand, and increase production.
For example, gas analyzers can be utilized to track the levels of byproducts, which can be compressed and sold as a byproduct, resulting in additional revenue for the refinery.
Another function of sensors in petroleum refineries is in the tracking of flue gas emissions.
Air fumes monitors record the levels of pollutants, such as carbon monoxide, in the emissions from the refinery's combustion devices.
This information enables refineries to improve their combustion processes, reduce their natural consequence, and fulfill with regulatory standards.
The use of gas analyzers in refinery plants also enables refineries to enhance their total Security, Well-being, and Ecology (SHE) efficiency.
By observing and controlling the quantities of hazardous fumes, operators can prevent accidents and close calls, reducing the risk of harm to staff, damage to equipment, and ecological contamination.
Furthermore, gas analyzers can be employed to record and document on SHE performance statistics, enabling refineries to determine areas for improvement and perform data-driven choices to optimize their SHE programs.
Recently years, progress in gas analytics equipment have led to the creation of new, more correct, and more portable gas monitors that are easier to setup and maintain.
Such new methods have enabled refineries to implement more complex monitoring and governance strategies, resulting in improved efficiency, minimized costs, and increased SHE performance.
To summary, process analyzers are a vital part of oil refinery operations, providing essential facts for monitoring and regulating the composition of process streams, improving refinery operations, and improving SHE performance.
Through exploiting the latest advances in scientific analysis innovation, refineries can guarantee safe, efficient, and successful operations, while also reducing their environmental impact and meeting with regulatory standards.
For information is essential for supervising and governing the refinery's efficiency processes, guaranteeing the security of the plant, and minimizing natural consequence.
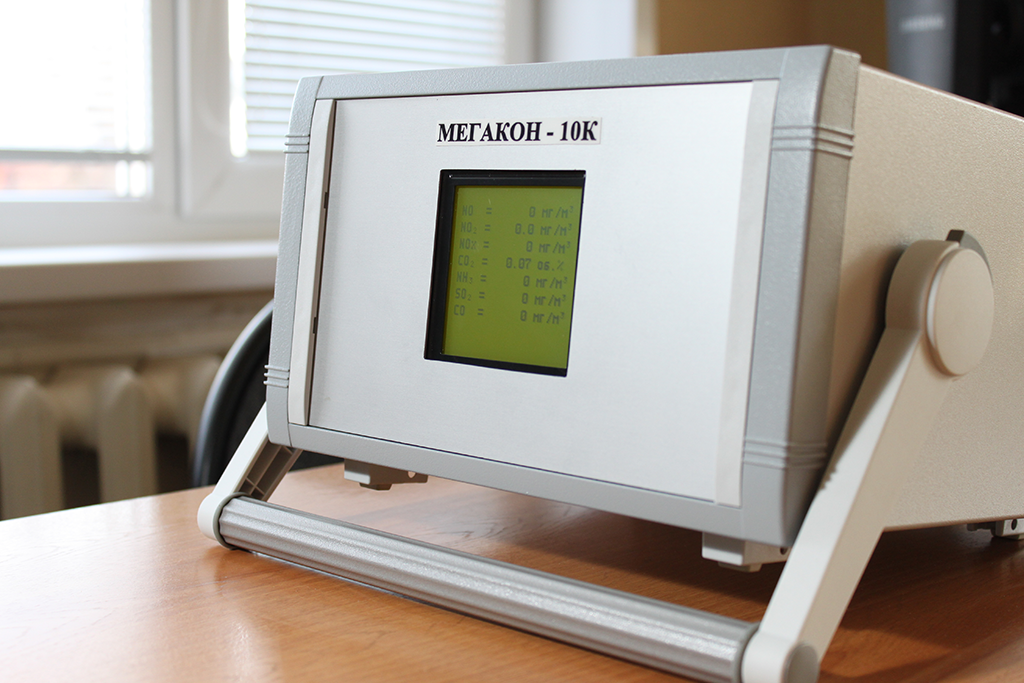
Process analyzers enable refineries to identify these gases in real-time data, enabling operators to perform corrective moves to prevent these issues.
In addition to controlling hazardous fumes, sensors also utilize a crucial role in optimizing refinery operations. Through examining the make-up of the medium, operators can spot opportunities to improve efficiencies, minimize energy demand, and increase production.
For example, gas analyzers can be utilized to track the levels of byproducts, which can be compressed and sold as a byproduct, resulting in additional revenue for the refinery.
Another function of sensors in petroleum refineries is in the tracking of flue gas emissions.
Air fumes monitors record the levels of pollutants, such as carbon monoxide, in the emissions from the refinery's combustion devices.
This information enables refineries to improve their combustion processes, reduce their natural consequence, and fulfill with regulatory standards.
The use of gas analyzers in refinery plants also enables refineries to enhance their total Security, Well-being, and Ecology (SHE) efficiency.
By observing and controlling the quantities of hazardous fumes, operators can prevent accidents and close calls, reducing the risk of harm to staff, damage to equipment, and ecological contamination.
Furthermore, gas analyzers can be employed to record and document on SHE performance statistics, enabling refineries to determine areas for improvement and perform data-driven choices to optimize their SHE programs.
Recently years, progress in gas analytics equipment have led to the creation of new, more correct, and more portable gas monitors that are easier to setup and maintain.
Such new methods have enabled refineries to implement more complex monitoring and governance strategies, resulting in improved efficiency, minimized costs, and increased SHE performance.
To summary, process analyzers are a vital part of oil refinery operations, providing essential facts for monitoring and regulating the composition of process streams, improving refinery operations, and improving SHE performance.
Through exploiting the latest advances in scientific analysis innovation, refineries can guarantee safe, efficient, and successful operations, while also reducing their environmental impact and meeting with regulatory standards.
- 이전글Who Else Wants To Take pleasure in Deepseek Ai 25.03.21
- 다음글Maintaining your bike's air filter is an vital aspect of bike maintenance that often gets overlooked. By maintaining your bike's air filter clean, you can improve its performance and gas mileage. In this article, we will provide you with some useful mot 25.03.21
댓글목록
등록된 댓글이 없습니다.